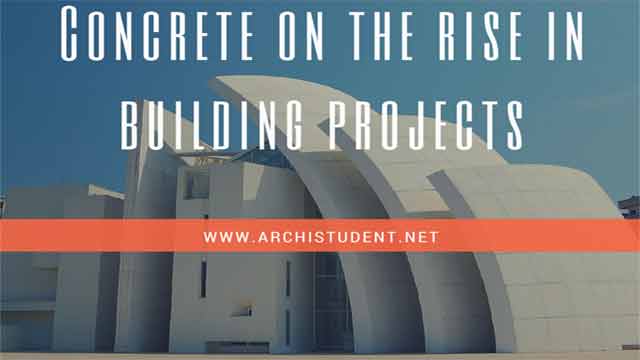
Concrete on the Rise in City Building Projects
While browsing on net for concrete constructions, I came across this very informative article. Hope it will be of some help you as well.
BY JOAN VOLLERO – Special to the Sun
March 29, 2007
Source: https://tinyurl.com/grrfrbz
Everyone who sees the new world headquarters of Barry Diller’s IAC is likely to see something different. Architect Frank Gehry’s first structure on Manhattan’s West Side Highway could be said to resemble billowing sails or a pleated skirt, but the real sleight is concealed: It is concrete, not steel, that makes up the building’s backbone.
The reinforced concrete slabs and tilted concrete columns were not part of the first blueprints. “It was originally designed by Gehry in steel,” the executive director of the New York Concrete Promotion Council, Carmine Attanasio, said. The group charged with boosting concrete’s presence in the city points to the IAC building as just one of several “conversions,” the industry’s term for buildings conceived in steel but that wind up with it in the finished product. Mr. Gehry changed his plans after an engineer, Vincent DeSimone of DeSimone Consulting Engineers, suggested he use concrete, Mr. Attanasio said.
Another such “conversion,” 505 Fifth Ave., peers over Bryant Park from across 42nd Street.
Ever since the terrorist attacks of September 11, 2001, concrete’s presence in New York has been on the rise. Due to concrete’s fireproofing qualities, it is especially being used in elevators, stairways, and other means of exit. It is also being used to insulate steel beams. “One of the advantages of concrete is it is an inert material. It doesn’t combust,” an engineer who is a member of the NYCPC, Michael Mota, said. “It can withstand two to three hours of fire without really a lot of damage.”
Constructed after September 11, the U.S. Mission to the United Nations at 45th Street and First Avenue is one New York building that opted for concrete from the start. Architects Gwathmey Siegel purposely constructed thick exterior walls using reinforced concrete, because the material can withstand car bombs and chemical or even biological terrorist attacks.
Speed is another factor in the decision to use it. “You can build structures, especially residential structures, faster, and occupy them sooner” with concrete, Mr. Mota said. The industry standard is to build at the rate of a floor every two days. “That’s something that’s unprecedented outside of New York City,” he said. “Usually, if you go to other parts of the country, concrete construction is on a five-day cycle.”
The Solaire and Tribeca Green are residential towers that rapidly rose in Lower Manhattan. Made of reinforced concrete plates, both received official LEED status from the U.S. Green Building Council. While the Tribeca Green offers such features as “rainwater recycling for landscaping and maintenance” (perhaps to offset the karmic cost of 24-hour valet parking and a “pram room”), the building’s concrete superstructure was also brought up to green standards. In the concrete mix, about 50% of the cement was replaced by slag, which significantly reduces carbon dioxide emission and requires less energy to produce, according to the Slag Cement Association.
It seems that not even Mother Nature herself can slow concrete’s forward march. Because concrete is sensitive to temperature, it can crack if exposed to excessive heat or cold after being poured. However, construction demands have transformed it into a year-round industry, with a few exceptions for the coldest days of the year.
In fact, the only thing threatening to freeze the concrete industry is concern over supply. Two years ago, a shortage of portland cement, an ingredient in concrete, led to a concrete shortage in New York City. This shortage coincided with an unprecedented building boom in China, which is where a lot of cement was being diverted. Tishman Construction Corp. was initially concerned about finding enough concrete to build the reinforced core of 7 WTC (the building’s superstructure is steel), but concrete producers and suppliers rose to the task.
Since then, producers have had a chance to catch up and are better equipped to meet China and India’s growing appetite for building materials. America is also boosting its supply by importing about 20% of the cement it consumes yearly. “Right now, we’re consuming everything we’re producing. There is no surplus,” Mr. Mota said. “Whatever is being produced is being consumed.”
The New York Building Congress’s 2006–08 construction shows there is reason for concern over building material supply and the means of carting it. Its biannual report lists the rising costs of commodities such as concrete and steel and the high price of fuel as causes for concern. There are also questions about the number of qualified contractors able to execute multiple overlapping construction schedules. “Lower Manhattan over the next several years has more construction planned than maybe has ever occurred in a square mile of a city,” the president of the construction and real estate trade group, Richard Anderson, said.
Despite of the daunting number of stadiums, skyscrapers, condominiums, and transit hubs slated for the coming years, the concrete industry is optimistic.
“There may be here or there … ” Mr. Mota said, stopping himself, “I don’t want to use the word ‘shortages,’ because that alarms people, but I think all in all we’ll be able to meet the demand.”